There’s something so satisfying about creating your own clothes, especially when it’s a timeless piece like a denim jacket. It’s not just about the finished product—it’s the process of stitching together fabric, adding personal touches, and knowing you’ve made something truly unique. If you’ve ever dreamed of crafting your own denim jacket from scratch, you’re in the right place.
Materials And Tools You Will Need
Creating a denim jacket requires the proper materials and tools to achieve a polished, durable result. Here’s what you’ll need to get started.
Essential Sewing Tools
- Sewing Machine
A sturdy sewing machine capable of handling thick fabrics like denim is crucial. Look for one with adjustable stitch length and a heavy-duty needle option.
- Denim Needles
Use size 90/14 or 100/16 denim needles. These are strong enough to penetrate thick layers without breaking.
- Thread
Polyester or denim-specific thread adds durability. Choose a color that blends with or contrasts the fabric, depending on your design.
- Scissors and Rotary Cutter
Sharp fabric scissors ensure clean cuts, while a rotary cutter simplifies precise pattern cutting.
- Measuring Tape and Ruler
These tools help maintain accurate dimensions for your jacket pieces.
- Pins and Clips
Clips work better than pins for holding multiple thick fabric layers.
- Seam Ripper
A seam ripper is indispensable for correcting mistakes quickly.
- Iron and Pressing Tools
Use an iron to press seams for a professional finish. A tailor’s ham or seam roll aids in pressing curves.
Selecting The Right Denim Fabric
- Fabric Weight
Choose medium to heavy-weight denim (8-14 oz) for structure and durability. Lightweight denim lacks the stiffness needed for a jacket.
- Stretch vs. Non-Stretch
Non-stretch denim offers a classic look, while stretch denim adds comfort. For first-timers, non-stretch denim is easier to sew.
- Color and Finish
Indigo, black, or raw denim works well for jackets. Washed or distressed finishes suit a vintage aesthetic.
- Prepping the Fabric
Wash and dry the denim before sewing to prevent future shrinkage and ensure colorfastness.

These materials and tools simplify the creative process and ensure the final garment looks and feels professional.
Preparing Your Denim Fabric
Getting your denim fabric ready is a key step to creating a durable, professional-looking jacket. Careful preparation ensures accuracy and prevents common issues during sewing.
Measuring and Cutting the Fabric
Accurate measurements are essential for proper garment fit. I use a clear measurement grid and a tailor’s measuring tape to measure the pattern pieces on the denim. Pinning the pattern pieces securely to the fabric avoids shifting during cutting.
For cutting, I rely on heavy-duty shears designed for thicker materials like denim. Rotary cutters can also work well for precise, straight cuts. Leaving a 0.5-inch seam allowance around each pattern piece gives room for sewing.
Pre-washing the Denim
Pre-washing stabilizes denim by eliminating shrinkage and excess dye. I wash the fabric in cold water without fabric softener to maintain its texture. Air drying or using a low tumble-dry cycle reduces wear on the material.
« Making a Quilted Tote Bag: A Detailed Guide to Crafting Your Perfect Handmade Accessory
Master Sewing a Baby Blanket: A Soft Project That’s Easy, Affordable, and Full of Love »
I also iron the denim after it’s dried to smooth any creases before sewing. Pressing the fabric ensures clean lines for accurate cutting and stitching.
Step-By-Step Sewing Process
Creating a denim jacket involves precise steps to ensure the final piece is both durable and stylish. Each step adds structure and detail, transforming fabric into a functional garment.
Creating The Pattern For Your Jacket
I start by choosing a pattern that fits my desired style—classic, oversized, or cropped. Using a store-bought commercial pattern simplifies the process, but drafting a custom one ensures a perfect fit. I trace the pattern pieces onto durable paper, including seam allowances and markings for darts, pockets, and button placements. Cutting each piece carefully maintains accuracy and symmetry for a professional finish.
Assembling The Body Of The Jacket
I begin constructing the jacket by stitching the back and front panels. Pinning the pieces together with the right sides facing outward ensures clean seams. Using a sturdy stitch—such as a straight stitch followed by a flat-felled seam—secures the fabric while preventing fraying. I focus on aligning shoulders, side seams, and armholes properly, as they’re the jacket’s foundation. Adding pockets, flaps, and decorative stitching at this stage embeds character into the design.
Adding Sleeves And Collar
Attaching sleeves starts with matching the sleeve cap to the armhole, pinning notches carefully to avoid puckering. I sew the seams with precision and finish with a double topstitch for added durability and aesthetics. For the collar, I cut two identical pieces, sew them together along the edges, and flip them right side out before attaching to the neckline. Ensuring neat topstitching on the collar provides a polished appearance while holding its shape.
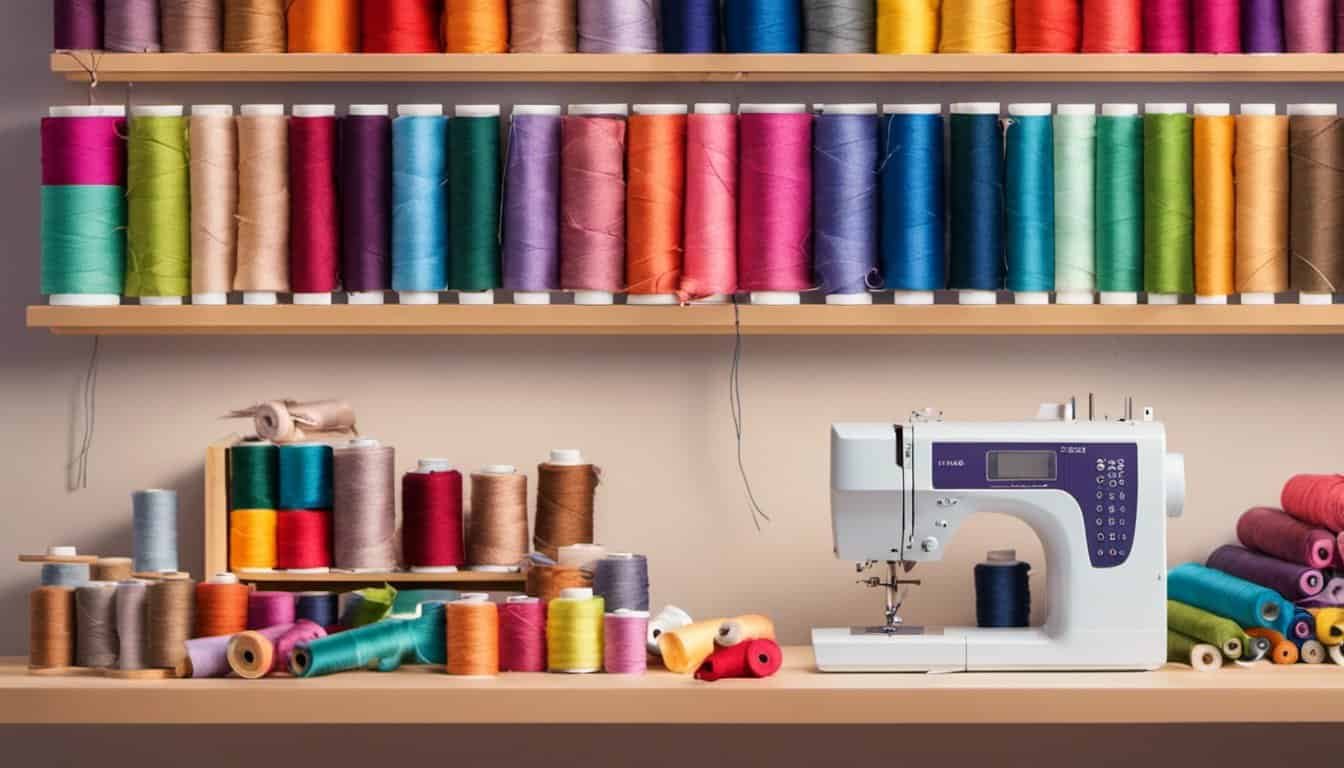
Finishing Touches: Buttons, Zippers, And Hemming
Adding closure elements enhances the jacket’s functionality. I use a quality buttonhole foot on my sewing machine to sew buttons, aligning them with marked placements for a balanced look. If using a zipper, I ensure it’s evenly sewn with matching thread. Hemming the jacket involves folding and pressing the raw edges, then sewing a clean line to secure the fabric. A final topstitch along key seams reinforces durability and completes the professional aesthetic.
Tips And Tricks For Working With Denim
Denim is durable but can be challenging to work with due to its thickness and stiffness. I’ve gathered essential tips to make sewing your denim jacket easier and more efficient.
Handling Thick Seams
Thick seams can be tough to sew without creating uneven or bulky results. I recommend using a denim needle, typically size 90/14 or 100/16, as it’s designed to penetrate thick fabrics smoothly. A walking foot helps evenly feed the fabric layers, reducing shifting.
Trimming seam allowances can significantly reduce bulk. For instance, after sewing a seam, trim one side down to half its width before folding. If a flat-felled seam is part of your design, press thoroughly with a hot iron to ensure it lays flat. Additionally, increasing your stitch length slightly, around 3-4mm, improves stitching through thicker sections.
Avoiding Common Mistakes
Common mistakes can compromise the look and durability of your denim jacket. Skipping proper fabric preparation leads to issues like shrinkage or uneven coloring. Always pre-wash and dry your denim to preempt these problems.
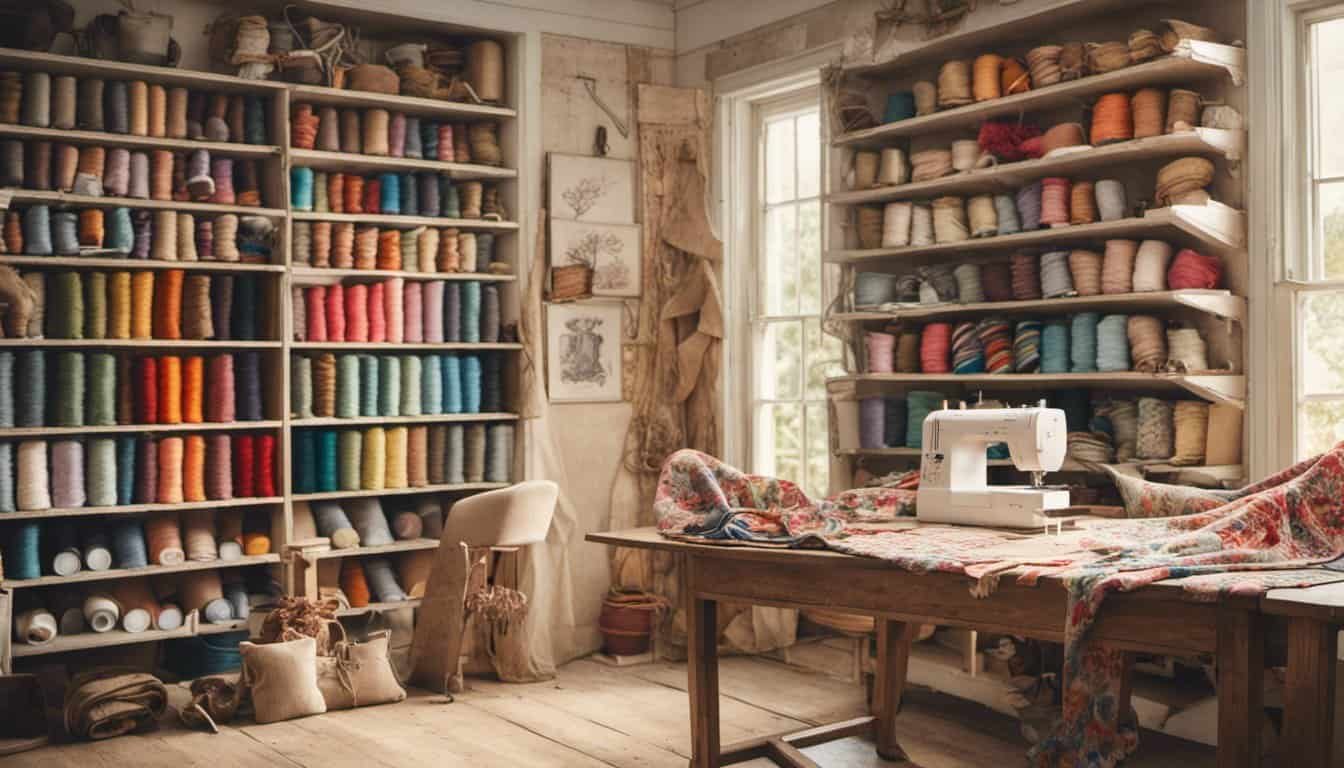
Rushing through seams often results in puckering or misaligned pieces. Double-check your pattern alignment before stitching, and pin or clip the layers securely, especially on corners or curves. Testing on scrap denim first ensures you’re using the proper tension, needle, and stitch settings.
Lastly, avoid using weak thread. Heavy-duty polyester or topstitching thread strengthens both seams and decorative stitching. If you sew too quickly, the fabric might not feed evenly, so keep a steady pace for clean, professional results.
Styling Your Handmade Denim Jacket
Customizing your denim jacket adds character and reflects your personal style. I focus on simple yet effective techniques that elevate the look of the finished piece.
Adding Embellishments
Embroidery designs, iron-on patches, or fabric paints create visual interest. I often use floral embroidery patterns on the back panel or sleeve cuffs for a chic touch. Patches featuring vintage graphics or slogans work great for bold, edgy styles.
Playing with Distressing
A distressed look transforms a plain jacket into a trendy statement piece. Sandpaper and a razor blade create controlled fraying at hemlines or pocket edges. I ensure balance by keeping the distressing subtle and focused on key areas.
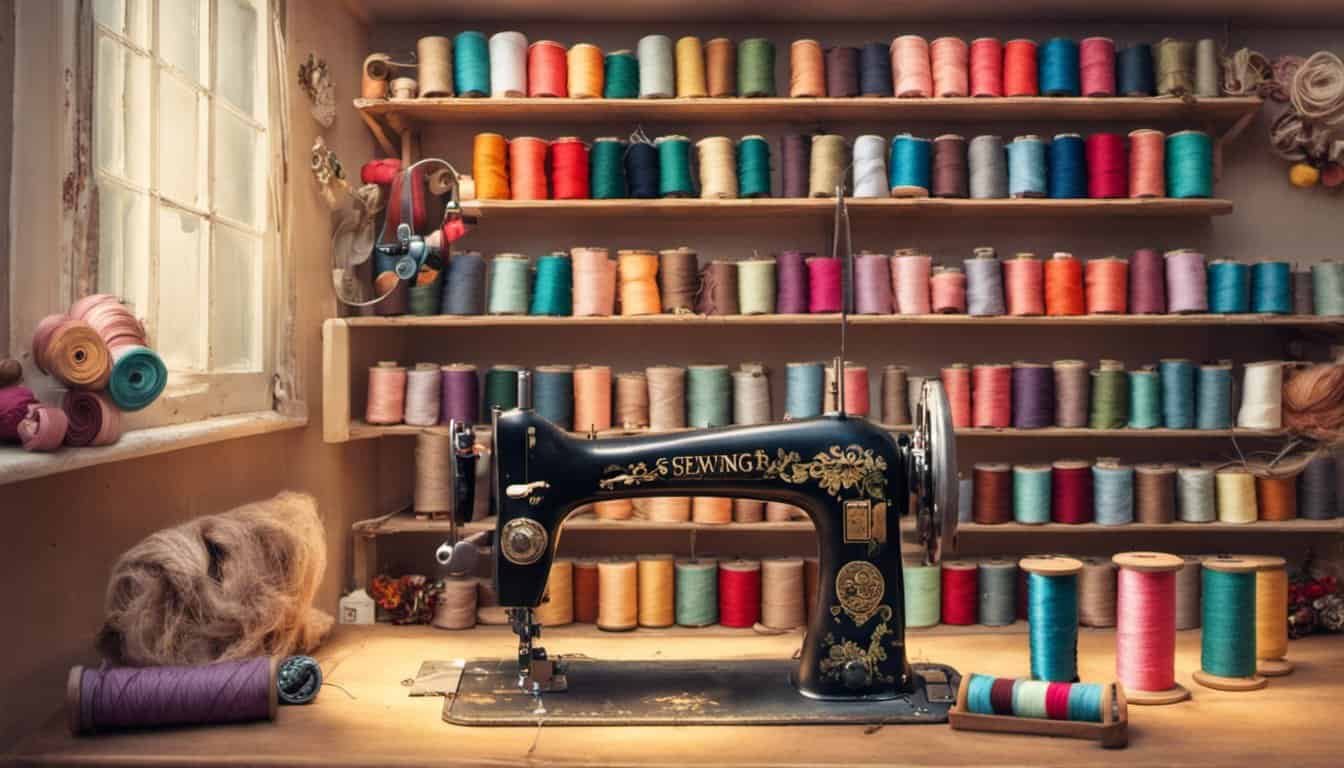
Experimenting with Wash Effects
Bleach washing or tie-dye techniques bring unique gradients or patterns to denim. I achieve a soft gradient by applying diluted bleach with a sponge, focusing on the shoulders or seams. For tie-dye, elastic bands section the jacket before submerging it in a bleach mixture.
Mixing Fabrics
Incorporating other fabrics, like plaid or leather, gives extra texture. I’ve added plaid patches to elbow areas or replaced a back panel with leather for a punk-inspired vibe. Stitching the fabric securely with strong thread ensures durability.
Accessorizing the Jacket
Unique buttons, zippers, and chains enhance the jacket’s appeal. Large copper buttons create a vintage aesthetic, while chains attached to pockets or hems add an alternative edge. I sometimes add these elements using pliers for precision in placement.
Personalizing the Fit
Altering the fit tailors the jacket even more to your taste. Cropping the hem or tapering the sleeves creates modern silhouettes. I measure carefully before altering and use a sharp rotary cutter for smooth edges.
Styling choices turn a handmade denim piece into a true one-of-a-kind garment.

Conclusion
Sewing a denim jacket from scratch is such a fulfilling journey. Not only do you get to create something functional and stylish, but you also end up with a piece that’s uniquely yours. The process may have its challenges, but the reward of wearing something you made with your own hands is unmatched.
Whether you’re adding personal touches or experimenting with creative techniques, the possibilities are endless. Take your time, enjoy the process, and don’t be afraid to let your creativity shine. Your handmade denim jacket will not only reflect your style but also your dedication and craftsmanship.