There’s something so satisfying about creating your own pair of jeans. From choosing the perfect fabric to stitching every seam, it’s a process that feels both creative and empowering. Sure, jeans might seem tricky to sew, but with the right approach, they’re totally doable—even for someone who’s not a seasoned pro.
I’ve learned that sewing jeans isn’t just about making pants; it’s about crafting something that fits you perfectly. No more tugging at waistbands or dealing with too-short hems! Whether you’re customizing your favorite style or tackling a full-on DIY project, sewing jeans can be a fun and rewarding adventure.
Understanding The Basics Of Sewing Jeans
Sewing jeans starts with mastering the essentials and making informed choices. With the right preparation, creating custom-fit pants becomes an achievable task.
Essential Supplies And Tools
Proper tools make sewing jeans manageable and efficient. A heavy-duty sewing machine supports sturdy denim stitching. Denim needles, typically size 90/14 or 100/16, handle thick layers without breaking. Polyester thread, in a 30-weight or similar, ensures strong seams. Cutting tools like rotary cutters or sharp scissors deliver clean edges. A sturdy ruler or straight edge assists with precise measurements, while a seam ripper allows for error correction. For durable finishes, invest in topstitching thread and brass rivets.
Choosing The Right Fabric
Select fabrics based on the desired outcome. Non-stretch denim, in 10- to 14-ounce weights, works well for structured, classic jeans. Stretch denim with 2-3% elastane suits projects requiring flexibility, such as skinny or fitted styles. Lightweight denim, weighing 8-10 ounces, fits casual designs like relaxed pants or summer jeans. Consider fabric colors and washes to match your style preferences. Always pre-wash denim to prevent shrinkage after sewing.
Preparing Your Pattern And Measurements
Accurate measurements and a well-chosen pattern ensure your jeans look great and fit perfectly. Starting with these steps makes the entire process smoother.
Taking Accurate Measurements
I always measure precisely before cutting fabric to avoid mistakes. Use a flexible measuring tape and write down key dimensions: waist, hips, rise, inseam, and thigh circumference. Measure the waist at the narrowest point, hips at the fullest part, and the rise from the crotch to the waistband. For the inseam, measure from the crotch to the desired hemline. Record thigh circumference around the widest part of the upper leg.
Verify measurements twice for accuracy, especially when working with stretch denim, as it may alter the fit. For a looser or more tailored fit, consider adding or subtracting a small amount from the measurements before finalizing.
Choosing Or Creating A Jeans Pattern
The right pattern depends on style preference and skill level. Ready-made jeans patterns from trusted brands like McCall’s or Burda simplify the process and come with clear instructions. These patterns often include style variations like straight, skinny, or relaxed-leg designs.
For a custom pattern, I adjust a standard one to match unique measurements. Trace the base pattern onto tracing paper, then align it with the recorded dimensions. Add seam allowances (typically 5/8 inch) and extra for features like waistbands or hems. If modifying elements like pocket placement or leg width, test the adjustments with a muslin mock-up to check the fit before cutting the denim.
Step-By-Step Guide To Sewing Jeans
Sewing jeans involves careful planning and precision to create a durable, well-fitted garment. Following these steps ensures a smooth process.
Cutting The Fabric
Cutting the fabric lays the foundation for well-fitted jeans. I recommend laying your denim flat on a clean surface after ironing it. Pin your pattern pieces securely to prevent shifting. Use sharp fabric scissors or a rotary cutter to achieve clean edges, especially along the grainline. If working with stretch denim, take extra care to avoid distortion by handling the fabric gently. Mark notches and darts carefully using tailor’s chalk or a washable fabric pen.
Constructing The Seams
Strong seams are essential for jeans that last. For step one, sew the inseams and outseams using a straight stitch. Choose a heavy-duty polyester thread and a denim needle for better penetration through thick layers. To reinforce the seams, I use a flat-felled technique, trimming one seam allowance and folding the other over it before topstitching. For curved areas like the crotch, clip the seam allowance slightly to help it lay flat. Adjusting the machine’s tension helps achieve smooth, even stitches.
Adding Pockets And Details
Pockets enhance the functionality and style of your jeans. Start by sewing the front pocket bags to the pocket facings, then attach them to the front leg panels. For back pockets, topstitch them onto the rear panels, ensuring they’re symmetrical. I add rivets at stress points to increase durability. For the waistband and belt loops, use double topstitching to give a professional finish. Embellishments like contrast stitching or embroidery can add a personal touch to your jeans.

Perfecting The Fit
A well-fitted pair of jeans not only looks great but also feels comfortable. Adjustments to the waistband, length, and taper ensure every detail matches your body and style preferences.
Adjusting The Waistband
Getting the waistband just right is essential for comfort and support. I start by checking how the waistband aligns with my natural waist. If it’s too tight, I insert a small section of elastic or add fabric panels to expand the size discreetly. For jeans that feel loose, I take in the waistband by opening the center back seam, removing excess material, and stitching it back with a strong, reinforced seam.
Matching the waistband curve to your body shape makes a big difference. I recommend making small changes gradually and fitting the jeans after each adjustment. Using pins or a basting stitch helps temporarily hold adjustments while ensuring the fit is accurate before final sewing.
Altering Length And Taper
The right length enhances the proportion of jeans to your body. I measure the desired length while wearing the jeans with shoes for accuracy. After marking the new hemline, I cut off the excess fabric, leaving an extra 1-1.5 inches for a double-fold hem, which prevents fraying and creates a polished finish.
When tapering, I reshape the legs to follow my preferred style, whether straight, slim, or skinny. I turn the jeans inside out, mark the excess width with chalk along the inseam or outer seam, and sew gradually to blend the new line into the original seam. Using a denim needle ensures the stitching stays clean and sturdy.
« How to Sew a Tiered Skirt with Layers: Easy DIY Guide for Stunning Results
How to Sew a Bow Tie for Any Occasion: Easy DIY Steps to Save Money and Look Stylish »
Final pressing with a steam iron gives both the hems and taper adjustments a professional appearance. Taking the extra time to refine these details elevates the overall fit and showcases your personal craftsmanship.
Finishing Touches
Finishing touches elevate handmade jeans from good to great. These details add style, polish, and durability while showcasing craftsmanship.
Topstitching Techniques
Topstitching reinforces seams and adds decorative flair. I recommend using a heavier thread, like topstitching thread, and adjusting the stitch length to 3-4mm for clean, even stitches. Keep the fabric taut while sewing to avoid puckering. Common areas for topstitching include the waistband, pockets, side seams, and hems. Doubling up rows of stitches can highlight these areas further. To ensure symmetry, I always mark stitching lines lightly with chalk or a fabric marker before starting. When the design allows it, contrasting or color-coordinated threads can be used to personalize the look.
Adding Hardware Like Rivets and Buttons
Adding hardware strengthens stress points and gives jeans a professional finish. Rivets, commonly placed on pocket corners, prevent tearing in high-stress areas. To install them, use a hand press or a rivet setting tool, ensuring exact alignment to avoid misplacement. For buttons, jeans buttons are a solid choice due to their durability. I use an awl or small hole punch to create openings precisely where the pattern indicates, then hammer the button into place. Verify that all hardware is securely attached to ensure long-lasting wear. For a modern twist, consider matte-finish hardware or unique shapes.
Tips For Success
Crafting high-quality jeans takes patience and attention to detail. Focusing on precision and avoiding common pitfalls ensures professional results while preserving your finished project for years.
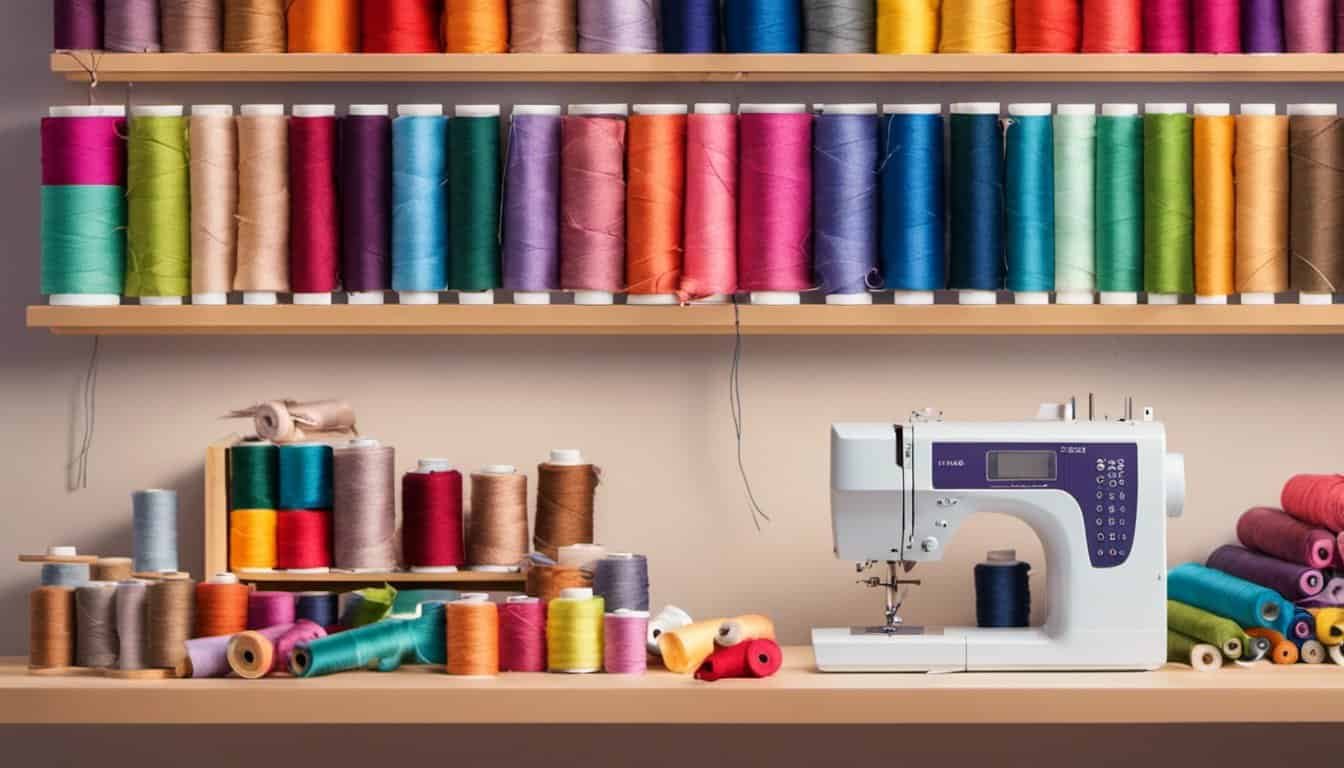
Common Mistakes To Avoid
- Skipping Fabric Pre-Wash
Pre-washing denim is essential to prevent shrinkage after sewing. The fabric can shrink significantly, disrupting fit and design, so always wash and dry it beforehand.
- Using Incorrect Needle and Thread
Standard needles and cotton threads aren’t designed for denim. Heavy-duty needles, like size 90/14 or 100/16, and polyester thread resist breaking, ensuring cleaner stitches through thick fabric.
- Improper Seam Finishing
Raw denim edges unravel if not properly sealed. Use techniques like overlocking, zigzag stitching, or flat-felled seams to reinforce edges and maintain durability.
- Rushing Through Topstitching
Uneven or distorted topstitching distracts from the finished look. Slow down and use a guide to keep the stitching straight, especially if using contrasting threads.
- Forgetting to Test Fit
Skipping a mock-up or mid-project fitting increases risks of poor fit. Always pin or baste pieces together for test fittings to identify adjustments before final stitching.
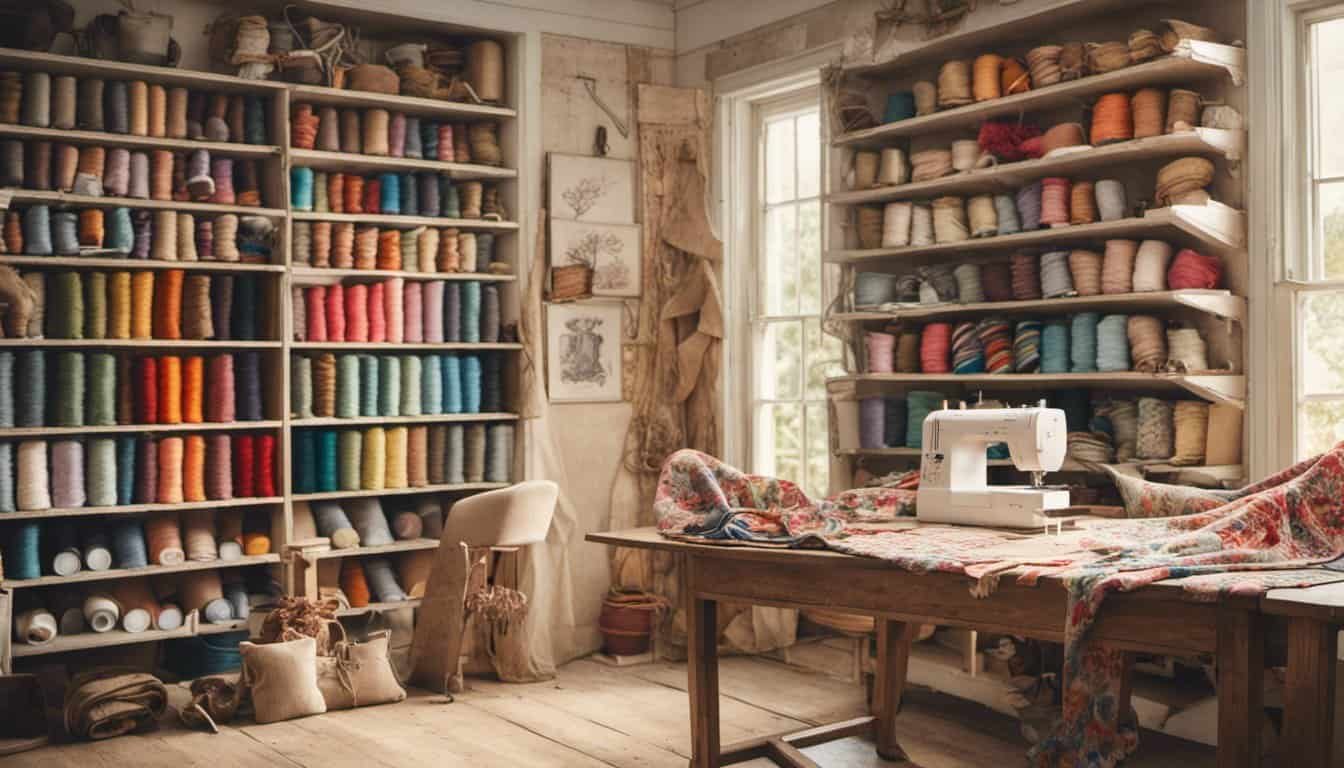
Preserving Your Finished Jeans
- Wash Sparingly
Frequent washing fades denim and weakens fibers. Spot cleaning minor stains and using cold washes with a gentle detergent keeps the jeans fresh while protecting the fabric.
- Avoid High Heat
High-temperature drying causes shrinkage and damages fibers. Line drying or using a low-heat setting in the dryer maintains the jeans’ structure and fit.
- Reinforce Frequently Used Areas
Stress points like pockets and crotch areas wear down faster. Adding extra stitches, backing material, or replacing rivets maintains durability over time.
- Store Properly
Hanging jeans protects the fit and prevents creasing, especially for pairs using stretch denim. Fold non-stretch jeans loosely to avoid creating permanent lines.
These tips ensure your handmade jeans remain sturdy and stylish, reflecting the effort that went into each stitch.
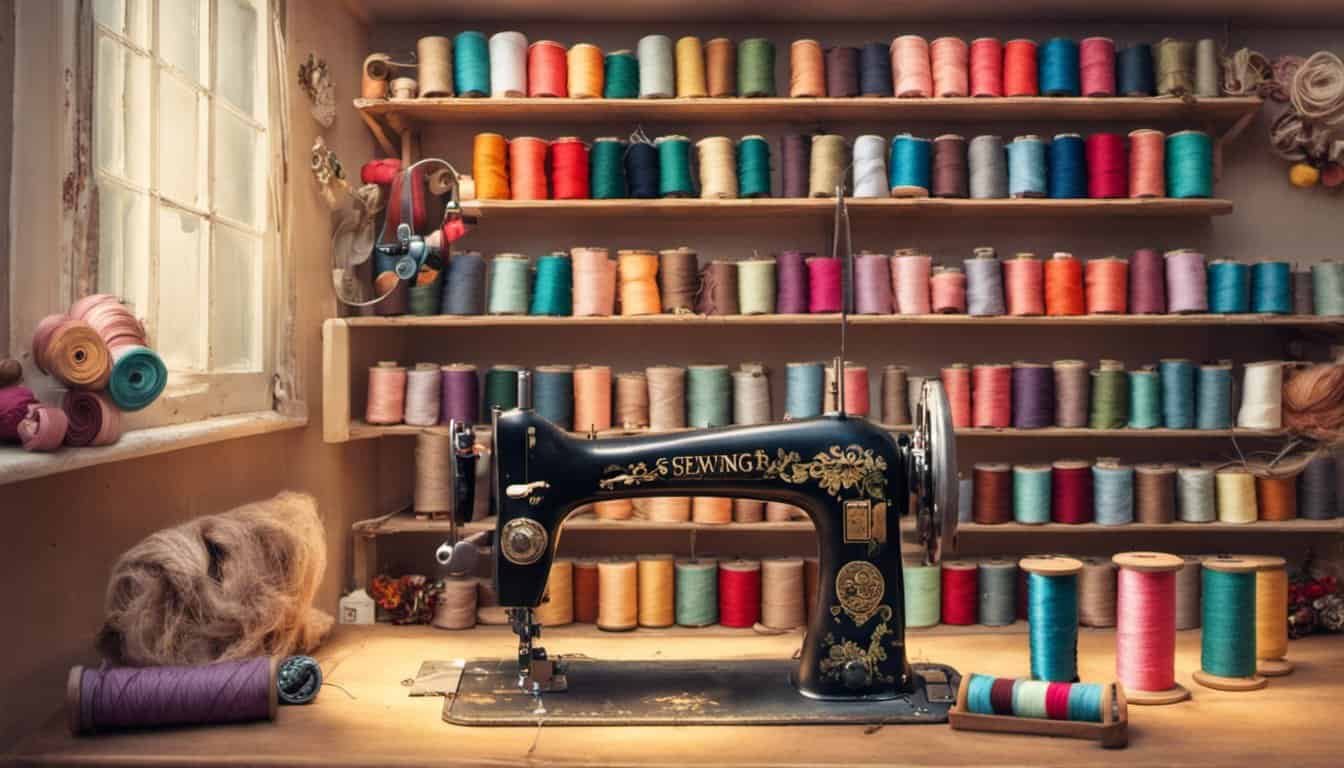
Conclusion
Sewing your own jeans is such a fulfilling journey. It’s not just about creating a pair of pants; it’s about crafting something that’s uniquely yours and fits you perfectly. Sure, it takes time and effort, but the reward of wearing jeans you made with your own hands is absolutely worth it.
Remember to enjoy the process, embrace the learning curve, and celebrate the little victories along the way. With the right tools, patience, and attention to detail, you’ll be amazed at what you can achieve. Your perfect pair of jeans is just a few stitches away!